Safety Bulletin
Safety Bulletin
Why Time-Boxed Inspections Are a Dangerous Practice for Utility Stringing Lines
Why Time-Boxed Inspections Are a Dangerous Practice for Utility Stringing Lines



Best Practices for Safer, More Reliable Operations
Scope has collaborated closely with leading utility companies and contractors to compile a comprehensive set of best practices, drawn directly from the expertise of those who work in the field every day. This best practices guide covers a wide range of critical topics, from recommended inspection frequencies to mid-line repairs and detailed inspection procedures.
By working alongside industry professionals, Scope has ensured that the guide reflects real-world conditions and practical solutions. Designed as a flexible tool, companies can choose to adopt it in part or as a whole, tailoring it to fit their unique operational needs while enhancing the safety and reliability of their stringing lines.
Visit our Best Practices Page to access expert guidance from industry leaders, tailored to meet your operational needs.
In the world of utility stringing operations, safety, reliability, and efficiency are paramount. Utility companies and contractors rely on strong, dependable stringing lines to handle the immense tension and stress involved in pulling conductors across long distances, often under challenging environmental conditions.
In the world of utility stringing operations, safety, reliability, and efficiency are paramount. Utility companies and contractors rely on strong, dependable stringing lines to handle the immense tension and stress involved in pulling conductors across long distances, often under challenging environmental conditions.
However, despite the critical nature of these operations, many companies continue to rely on outdated time-boxed inspection schedules to determine when their stringing lines are inspected. This practice, while seemingly convenient, is inherently dangerous.
However, despite the critical nature of these operations, many companies continue to rely on outdated time-boxed inspection schedules to determine when their stringing lines are inspected. This practice, while seemingly convenient, is inherently dangerous.
A staggering 86% of stringing lines are overdue for inspection, meaning that the vast majority of utility operations may be using lines that are no longer fit for service. Time-boxed inspections — whether scheduled quarterly, biannually, or even annually — fail to take into account the frequency, intensity, or criticality of the line’s usage. This oversight can lead to catastrophic results, ranging from millions of dollars in downtime and equipment damage to serious injuries and even fatalities.
A staggering 86% of stringing lines are overdue for inspection, meaning that the vast majority of utility operations may be using lines that are no longer fit for service. Time-boxed inspections — whether scheduled quarterly, biannually, or even annually — fail to take into account the frequency, intensity, or criticality of the line’s usage. This oversight can lead to catastrophic results, ranging from millions of dollars in downtime and equipment damage to serious injuries and even fatalities.
It’s time to move beyond the limitations of time-based inspections and adopt a more proactive, event-based approach to stringing line safety.
It’s time to move beyond the limitations of time-based inspections and adopt a more proactive, event-based approach to stringing line safety.
The Hidden Risks of Time-Boxed Inspections
The logic behind time-boxed inspections seems straightforward: schedule inspections at regular intervals to ensure that stringing lines are in good working condition. But while this method offers consistency in scheduling, it overlooks a fundamental reality — stringing lines wear down based on how they are used, not how long they’ve been in service.
The logic behind time-boxed inspections seems straightforward: schedule inspections at regular intervals to ensure that stringing lines are in good working condition. But while this method offers consistency in scheduling, it overlooks a fundamental reality — stringing lines wear down based on how they are used, not how long they’ve been in service.
Traditional visual inspections only check one side of a line at high speeds, leading to risky, split-second decisions about its safety. Accurately determining line health has been difficult, often requiring breaking the line to assess residual strength. Wagner-Smith Equipment emphasizes the importance of identifying and resolving stringing line defects.
With one of the most expansive rental fleets across the continental United States, the inspection of stringing lines is a daily, ongoing effort at Wagner-Smith Equipment Co. Even with standardized procedures in place, manual visual inspections of these lines are extremely labor intensive and require technicians to maintain constant focus on the line while it being paid out and back in.
A line that experiences minimal tension and is used infrequently may remain in good condition for months or even years. However, a line that undergoes repeated high-tension pulls, is exposed to harsh operating conditions, or is subjected to heavy use will degrade much more quickly. By adhering to a rigid time-based schedule, companies risk overlooking serious wear and tear that occurs between inspections.
A line that experiences minimal tension and is used infrequently may remain in good condition for months or even years. However, a line that undergoes repeated high-tension pulls, is exposed to harsh operating conditions, or is subjected to heavy use will degrade much more quickly. By adhering to a rigid time-based schedule, companies risk overlooking serious wear and tear that occurs between inspections.
Traditional visual inspections only check one side of a line at high speeds, leading to risky, split-second decisions about its safety. Accurately determining line health has been difficult, often requiring breaking the line to assess residual strength. Wagner-Smith Equipment emphasizes the importance of identifying and resolving stringing line defects.
With one of the most expansive rental fleets across the continental United States, the inspection of stringing lines is a daily, ongoing effort at Wagner-Smith Equipment Co. Even with standardized procedures in place, manual visual inspections of these lines are extremely labor intensive and require technicians to maintain constant focus on the line while it being paid out and back in.
The consequences of this are severe. When a line fails under high tension, it’s akin to snapping a miles-long rubber band. The energy released by the line breaking can destroy everything in its path, including equipment, structures, and even lives. A broken line can bring operations to a halt, leading to days or weeks of downtime, not to mention the cost of repairs and replacements. In high-risk areas, such as energized corridors or over populated areas, a line failure can also cause widespread outages and other public safety concerns.
The consequences of this are severe. When a line fails under high tension, it’s akin to snapping a miles-long rubber band. The energy released by the line breaking can destroy everything in its path, including equipment, structures, and even lives. A broken line can bring operations to a halt, leading to days or weeks of downtime, not to mention the cost of repairs and replacements. In high-risk areas, such as energized corridors or over populated areas, a line failure can also cause widespread outages and other public safety concerns.
Traditional visual inspections only check one side of a line at high speeds, leading to risky, split-second decisions about its safety. Accurately determining line health has been difficult, often requiring breaking the line to assess residual strength. Wagner-Smith Equipment emphasizes the importance of identifying and resolving stringing line defects.
With one of the most expansive rental fleets across the continental United States, the inspection of stringing lines is a daily, ongoing effort at Wagner-Smith Equipment Co. Even with standardized procedures in place, manual visual inspections of these lines are extremely labor intensive and require technicians to maintain constant focus on the line while it being paid out and back in.
With 86% of lines overdue for inspection, the risk of such failures is alarmingly high.
With 86% of lines overdue for inspection, the risk of such failures is alarmingly high.
Traditional visual inspections only check one side of a line at high speeds, leading to risky, split-second decisions about its safety. Accurately determining line health has been difficult, often requiring breaking the line to assess residual strength. Wagner-Smith Equipment emphasizes the importance of identifying and resolving stringing line defects.
With one of the most expansive rental fleets across the continental United States, the inspection of stringing lines is a daily, ongoing effort at Wagner-Smith Equipment Co. Even with standardized procedures in place, manual visual inspections of these lines are extremely labor intensive and require technicians to maintain constant focus on the line while it being paid out and back in.
The Benefits of Event-Based Inspections
Rather than relying on arbitrary time frames, event-based inspections focus on the actual usage and conditions experienced by the stringing line. By scheduling inspections based on key operational events — such as after a major high-tension pull, before a particularly challenging project, or following exposure to extreme operating conditions — companies can better ensure that their lines are in optimal condition when they are most vulnerable.
Rather than relying on arbitrary time frames, event-based inspections focus on the actual usage and conditions experienced by the stringing line. By scheduling inspections based on key operational events — such as after a major high-tension pull, before a particularly challenging project, or following exposure to extreme operating conditions — companies can better ensure that their lines are in optimal condition when they are most vulnerable.
Event-based inspections offer several key benefits:
Event-based inspections offer several key benefits:
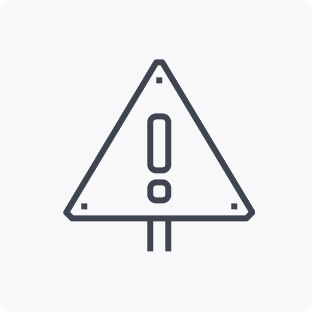
1
Increased Safety
Lines have been properly inspected and remediated at times when they are most likely to have experienced wear and tear, reducing the risk of catastrophic failures during critical operations.
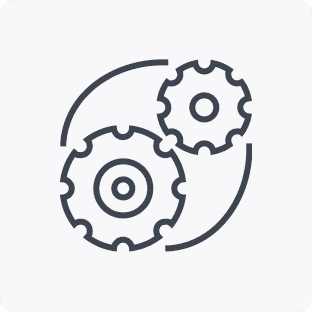
2
Optimized Maintenance
By inspecting lines after high-stress events, companies can identify damage or weakness before the next major operation, preventing downtime and costly repairs.
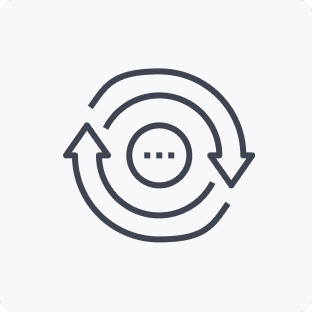
3
Flexibility
Event-based inspections allow companies to adjust their schedules based on actual usage, rather than sticking to rigid time frames that may not accurately reflect the line’s condition.
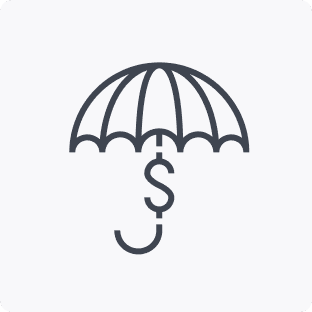
4
Cost Savings
Regular inspections between major operations help prevent unexpected failures, which can result in significant downtime, equipment damage, and potential legal liabilities. Proactively inspecting and maintaining lines reduces the overall cost of operations.
Why So Many Lines Are Overdue
Why are 86% of stringing lines overdue for inspection? One of the main reasons is logistical complexity. Traditionally, stringing line inspections have required companies to transport their pullers to maintenance facilities equipped with spooling capabilities. This process can be time-consuming and costly, leading some companies to delay inspections until they reach a scheduled time-boxed interval.
Why are 86% of stringing lines overdue for inspection? One of the main reasons is logistical complexity. Traditionally, stringing line inspections have required companies to transport their pullers to maintenance facilities equipped with spooling capabilities. This process can be time-consuming and costly, leading some companies to delay inspections until they reach a scheduled time-boxed interval.
However, this approach overlooks the fact that lines degrade at different rates depending on their usage. When companies delay inspections to fit into a predetermined schedule, they risk operating with lines that may already be compromised. This is especially true for high-use lines or those exposed to extreme conditions. Waiting for the next scheduled inspection could be disastrous.
However, this approach overlooks the fact that lines degrade at different rates depending on their usage. When companies delay inspections to fit into a predetermined schedule, they risk operating with lines that may already be compromised. This is especially true for high-use lines or those exposed to extreme conditions. Waiting for the next scheduled inspection could be disastrous.
How Scope Is Revolutionizing Line Inspections
At Scope, we recognize the challenges that come with scheduling and conducting regular stringing line inspections. That’s why we’re committed to making inspections more accessible and flexible for utility companies and contractors. Through our partnerships with service companies like SWOS, Carpenter Rigging, and UniRope, we are equipping these providers with Scope’s AI-driven inspection platform, allowing them to perform comprehensive inspections at your location or at conveniently located hubs across the U.S. and Canada.
At Scope, we recognize the challenges that come with scheduling and conducting regular stringing line inspections. That’s why we’re committed to making inspections more accessible and flexible for utility companies and contractors. Through our partnerships with service companies like SWOS, Carpenter Rigging, and UniRope, we are equipping these providers with Scope’s AI-driven inspection platform, allowing them to perform comprehensive inspections at your location or at conveniently located hubs across the U.S. and Canada.
This means that companies no longer have to rely on centralized inspection facilities or delay their inspections due to transportation and logistical hurdles. With Scope’s platform, inspections can be conducted on-site or at nearby service centers, making it easier than ever to schedule event-based inspections after major operations or high-tension events.
This means that companies no longer have to rely on centralized inspection facilities or delay their inspections due to transportation and logistical hurdles. With Scope’s platform, inspections can be conducted on-site or at nearby service centers, making it easier than ever to schedule event-based inspections after major operations or high-tension events.
By bringing inspections closer to your operations, we’re helping companies move away from dangerous time-boxed schedules and adopt a safer, more effective event-based approach to maintaining their stringing lines.
By bringing inspections closer to your operations, we’re helping companies move away from dangerous time-boxed schedules and adopt a safer, more effective event-based approach to maintaining their stringing lines.
Make the Shift to Event-Based Inspections
The data is clear: 86% of stringing lines are overdue for inspection, and time-boxed inspection schedules are putting utility companies and contractors at unnecessary risk. By shifting to event-based inspections, companies can ensure that their lines are inspected when they need it most — after high-tension pulls, between critical operations, and before challenging projects.
The data is clear: 86% of stringing lines are overdue for inspection, and time-boxed inspection schedules are putting utility companies and contractors at unnecessary risk. By shifting to event-based inspections, companies can ensure that their lines are inspected when they need it most — after high-tension pulls, between critical operations, and before challenging projects.
At Scope, we’re making it easier than ever to adopt event-based inspections, with our advanced inspection platform and a network of service providers ready to help you keep your operations safe and efficient. Don’t wait for the next scheduled inspection — start protecting your lines, your operations, and your people with event-based inspections today.
At Scope, we’re making it easier than ever to adopt event-based inspections, with our advanced inspection platform and a network of service providers ready to help you keep your operations safe and efficient. Don’t wait for the next scheduled inspection — start protecting your lines, your operations, and your people with event-based inspections today.
Want to dive in deeper?
Want to dive in deeper?
Download the safety bulletin and see how we can help in your next project.
Download the safety bulletin and see how we can help in your next project.
Download the safety bulletin and see how we can help in your next project.
Scope.
Cutting-edge Solutions for Rope Safety