Customer Case Study: Wagner-Smith Equipment Co.
Customer Case Study: Wagner-Smith Equipment Co.
Intelligent inspections are here.
Intelligent inspections are here.
Implementing AI Platform for Stringing Line Inspection for Wagner-Smith Equipment Co.
Implementing AI Platform for Stringing Line Inspection for Wagner-Smith Equipment Co.
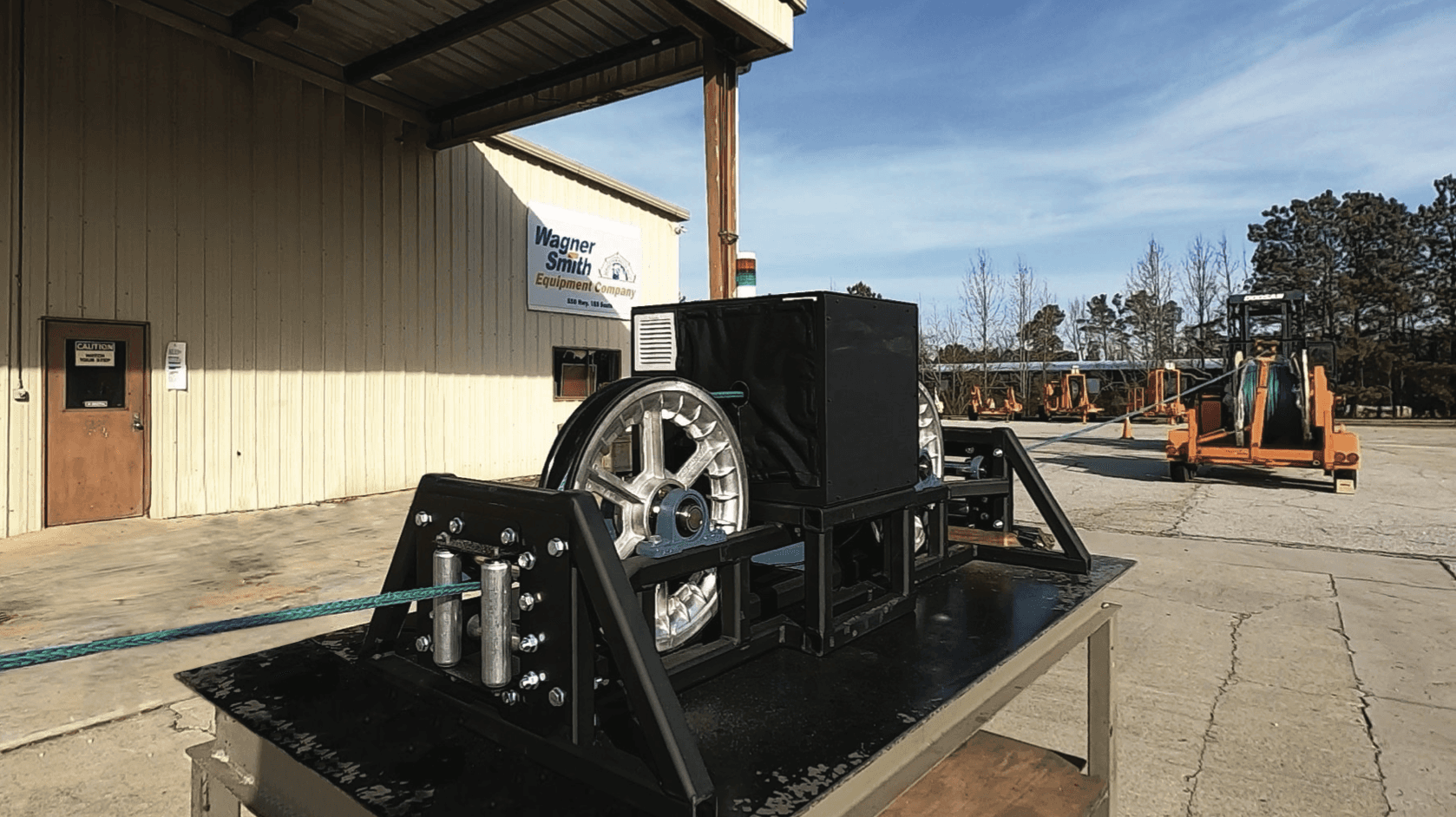
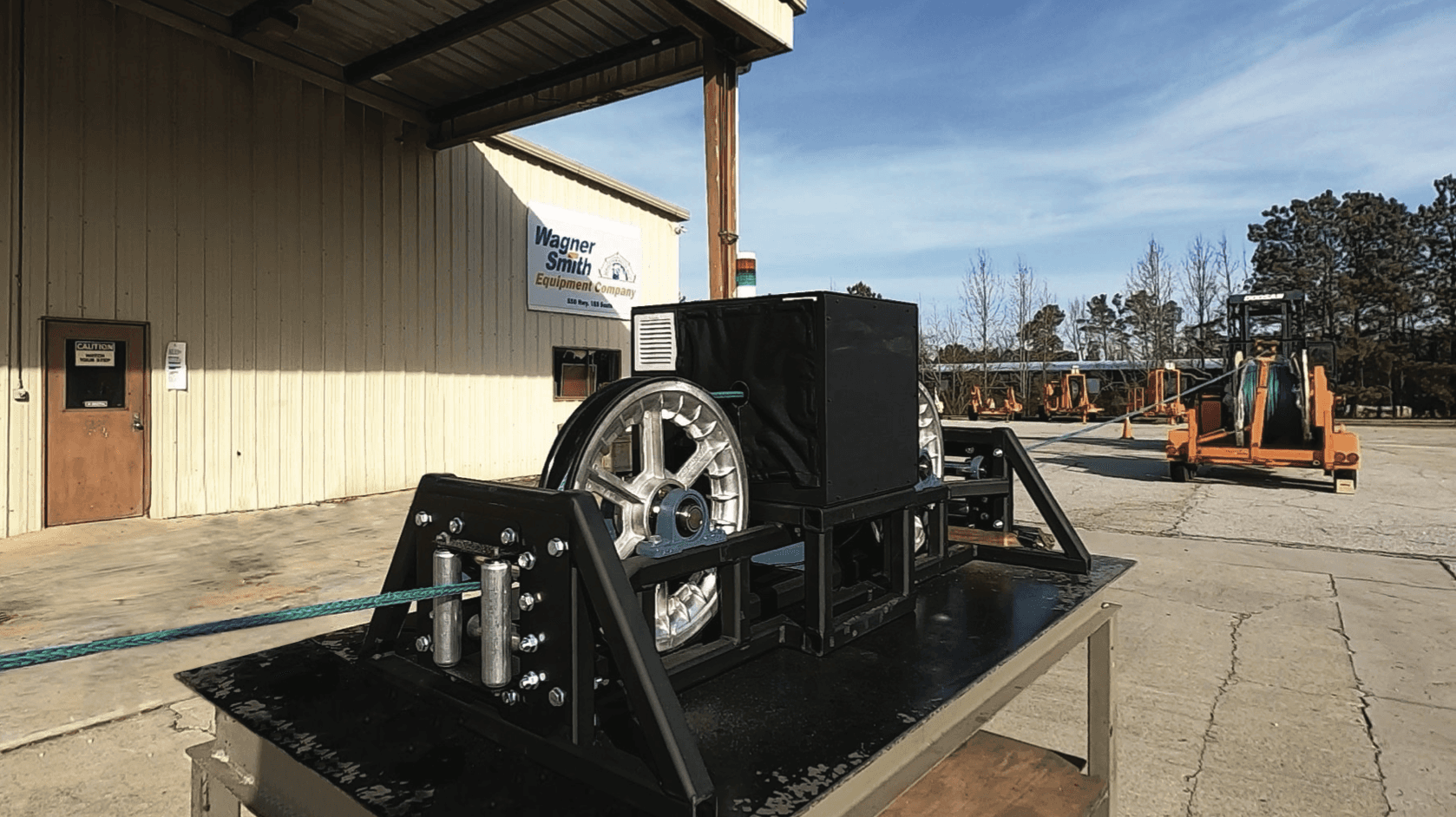
With one of the most expansive rental fleets across the continental United States, the inspection of stringing lines is a daily, ongoing effort at Wagner-Smith Equipment Co.
With one of the most expansive rental fleets across the continental United States, the inspection of stringing lines is a daily, ongoing effort at Wagner-Smith Equipment Co.
Even with standardized procedures in place, manual visual inspections of these lines are extremely labor intensive and require technicians to maintain constant focus on the line while it being paid out and back in.
Even with standardized procedures in place, manual visual inspections of these lines are extremely labor intensive and require technicians to maintain constant focus on the line while it being paid out and back in.
The Challenge
Traditional visual inspections only check one side of a line at high speeds, leading to risky, split-second decisions about its safety. Accurately determining line health has been difficult, often requiring breaking the line to assess residual strength. Wagner-Smith Equipment emphasizes the importance of identifying and resolving stringing line defects.
With one of the most expansive rental fleets across the continental United States, the inspection of stringing lines is a daily, ongoing effort at Wagner-Smith Equipment Co. Even with standardized procedures in place, manual visual inspections of these lines are extremely labor intensive and require technicians to maintain constant focus on the line while it being paid out and back in.
Traditional visual inspections only check one side of a line at high speeds, leading to risky, split-second decisions about its safety. Accurately determining line health has been difficult, often requiring breaking the line to assess residual strength. Wagner-Smith Equipment emphasizes the importance of identifying and resolving stringing line defects.
With one of the most expansive rental fleets across the continental United States, the inspection of stringing lines is a daily, ongoing effort at Wagner-Smith Equipment Co. Even with standardized procedures in place, manual visual inspections of these lines are extremely labor intensive and require technicians to maintain constant focus on the line while it being paid out and back in.
Traditional visual inspections only check one side of a line at high speeds, leading to risky, split-second decisions about its safety. Accurately determining line health has been difficult, often requiring breaking the line to assess residual strength. Wagner-Smith Equipment emphasizes the importance of identifying and resolving stringing line defects.
With one of the most expansive rental fleets across the continental United States, the inspection of stringing lines is a daily, ongoing effort at Wagner-Smith Equipment Co. Even with standardized procedures in place, manual visual inspections of these lines are extremely labor intensive and require technicians to maintain constant focus on the line while it being paid out and back in.
Gaining more precision around inspections and transparency into the line's quality was vital, particularly for mission-critical assets that directly affect operational safety, like stringing lines.
Gaining more precision around inspections and transparency into the line's quality was vital, particularly for mission-critical assets that directly affect operational safety, like stringing lines.
Gaining more precision around inspections and transparency into the line's quality was vital, particularly for mission-critical assets that directly affect operational safety, like stringing lines.
Primary Challenges
Accurately link abrasion levels to predicted residual break strength.
Detect cut strands, pulled strands, burns, debris, and splices with precision.
Measure distance traveled and continuously monitor line health.
Efficiently create comprehensive repair plans post-scan.
Easily review line scans and detect defects.
Generate automated reports and notifications based on scan data.
Primary Challenges
Accurately link abrasion levels to predicted residual break strength.
Detect cut strands, pulled strands, burns, debris, and splices with precision.
Measure distance traveled and continuously monitor line health.
Efficiently create comprehensive repair plans post-scan.
Easily review line scans and detect defects.
Generate automated reports and notifications based on scan data.
The Solution
Scope's system is powered by the Insight Engine, a highly trained deep learning neural network that identifies rope defects with 95% accuracy and predicts Residual Break Strength within +/-5%. Designed as a standalone unit placed between stringing machines, it uses multiple cameras to capture 360° views of the line, providing real-time feedback on rope health through a user-friendly interface.
Scope's system is powered by the Insight Engine, a highly trained deep learning neural network that identifies rope defects with 95% accuracy and predicts Residual Break Strength within +/-5%. Designed as a standalone unit placed between stringing machines, it uses multiple cameras to capture 360° views of the line, providing real-time feedback on rope health through a user-friendly interface.
The system continuously collects data during scans, analyzed by the Insight Engine and displayed on a tablet for quick decision-making. This data is securely stored online, allowing operators to review and plan repairs while fleet managers access real-time scans and reports, eliminating the need for manual inspection reports and streamlining the process.
The system continuously collects data during scans, analyzed by the Insight Engine and displayed on a tablet for quick decision-making. This data is securely stored online, allowing operators to review and plan repairs while fleet managers access real-time scans and reports, eliminating the need for manual inspection reports and streamlining the process.
The Scope platform captures and uploads images of line damage, making them accessible online. This promotes open communication and helps operators develop standardized repair protocols, streamlining processes.
The Scope platform captures and uploads images of line damage, making them accessible online. This promotes open communication and helps operators develop standardized repair protocols, streamlining processes.
The Scope platform captures and uploads images of line damage, making them accessible online. This promotes open communication and helps operators develop standardized repair protocols, streamlining processes.
The Wins & Successes
The benefits of implementing Scope were evident from the early development stages through the final handoff to operators. At the core of Scope's system is the Insight Engine, a deep learning neural network that has been rigorously trained to identify defects in rope with exceptional accuracy. Outcomes included:
The benefits of implementing Scope were evident from the early development stages through the final handoff to operators. At the core of Scope's system is the Insight Engine, a deep learning neural network that has been rigorously trained to identify defects in rope with exceptional accuracy. Outcomes included:
1st Day
The team automatically detected unknown issues, obtained a comprehensive data record, and received instant, accurate rope analysis.
75+
Unknown issues of different types were discovered on the lines in the first week.
100%
Traceability improved across the entire fleet, enabling programmatic tracking of line health on a line-by-line basis.
Integrating Scope's automated inspection system has reinforced Wagner-Smith's commitment to delivering secure, mission-critical stringing equipment by mitigating the limitations and risks of manual visual inspections. This system's failure analysis and serialized information capabilities have enabled efficient defect reviews, meticulous repair strategies, and comprehensive traceability.
Integrating Scope's automated inspection system has reinforced Wagner-Smith's commitment to delivering secure, mission-critical stringing equipment by mitigating the limitations and risks of manual visual inspections. This system's failure analysis and serialized information capabilities have enabled efficient defect reviews, meticulous repair strategies, and comprehensive traceability.
Scope's online platform has improved communication and visibility across Wagner-Smith's US locations, facilitating productive discussions with Utility Contractors. After a successful beta trial, Wagner-Smith deployed five Scope systems nationwide, offering efficient and accurate inspection services to its customers.
Scope's online platform has improved communication and visibility across Wagner-Smith's US locations, facilitating productive discussions with Utility Contractors. After a successful beta trial, Wagner-Smith deployed five Scope systems nationwide, offering efficient and accurate inspection services to its customers.
Innovating for a Safer Future
Innovating for a Safer Future
Scope's AI cloud-based app quickly identified previously undetected line defects, revealing anomalies invisible to manual inspectors and proving its effectiveness in automated defect detection and residual break strength prediction.
Scope's AI cloud-based app quickly identified previously undetected line defects, revealing anomalies invisible to manual inspectors and proving its effectiveness in automated defect detection and residual break strength prediction.
01
Maintaining a factor of safety
Manual visual inspection alone made it challenging for companies like Wagner-Smith to maintain their string- ing lines to a specific safety factor. In the past, their only option was to conduct break tests on select line segments as an indication of the strength of the unbroken line. However, with the introduction of Scope's automated inspection technology, Wagner-Smith can now consistently operate above a required safety factor for the residual strength of the line. This marks a historic milestone in the industry, as Wagner-Smith becomes the first OEM to offer such a high level of reassurance to its customers.
02
Verifiable Line History
03
Efficient Repair Planning

01
Maintaining a factor of safety
Manual visual inspection alone made it challenging for companies like Wagner-Smith to maintain their string- ing lines to a specific safety factor. In the past, their only option was to conduct break tests on select line segments as an indication of the strength of the unbroken line. However, with the introduction of Scope's automated inspection technology, Wagner-Smith can now consistently operate above a required safety factor for the residual strength of the line. This marks a historic milestone in the industry, as Wagner-Smith becomes the first OEM to offer such a high level of reassurance to its customers.
02
Verifiable Line History
03
Efficient Repair Planning

01
Maintaining a factor of safety
Manual visual inspection alone made it challenging for companies like Wagner-Smith to maintain their string- ing lines to a specific safety factor. In the past, their only option was to conduct break tests on select line segments as an indication of the strength of the unbroken line. However, with the introduction of Scope's automated inspection technology, Wagner-Smith can now consistently operate above a required safety factor for the residual strength of the line. This marks a historic milestone in the industry, as Wagner-Smith becomes the first OEM to offer such a high level of reassurance to its customers.
02
Verifiable Line History
03
Efficient Repair Planning

Looking Ahead
Looking Ahead
Looking Ahead



Scope envision
With Scope systems already deployed nationwide, a wealth of inspection data is being used to refine and train networks to accurately identify and predict potential issues. The possibilities for innovation in safer operations are boundless, including the ability to detect different types of splices and more nuanced degrees of damage, as well as leveraging tension data and line health to alert operators before critical thresholds are reached.
With Scope systems already deployed nationwide, a wealth of inspection data is being used to refine and train networks to accurately identify and predict potential issues. The possibilities for innovation in safer operations are boundless, including the ability to detect different types of splices and more nuanced degrees of damage, as well as leveraging tension data and line health to alert operators before critical thresholds are reached.
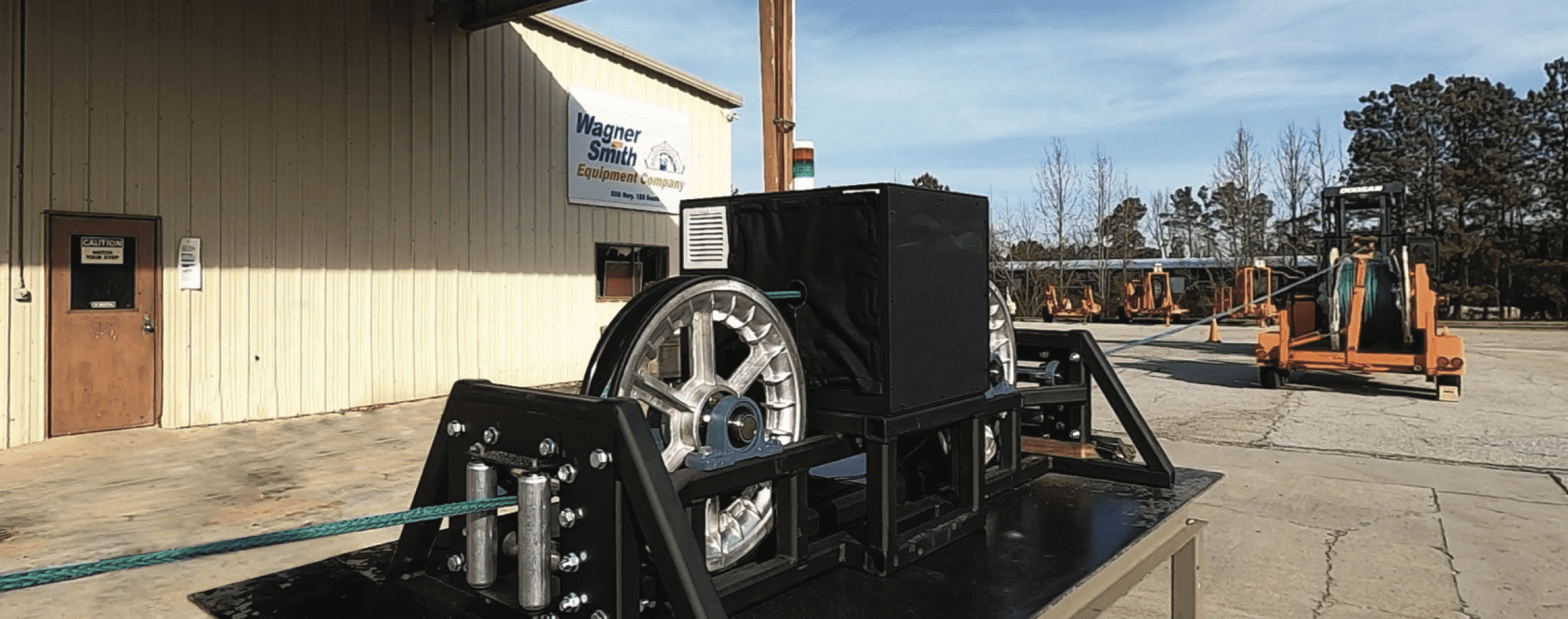
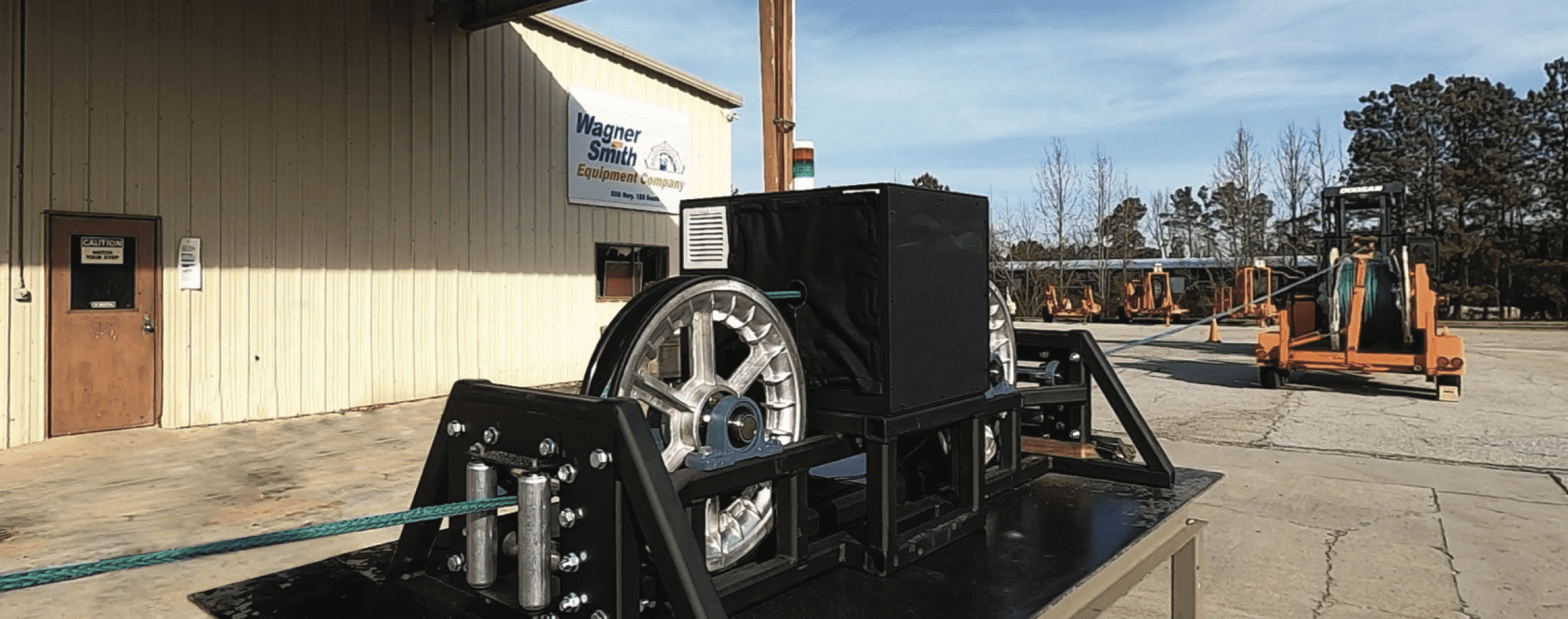
About Wagner - Smith
Established in 1917, Wagner-Smith Equipment has been synonymous with line-stringing equipment for as long as the industry has existed. As a trailblazer for generations, the company has excelled in designing, producing, renting, and servicing overhead and underground line-stringing equipment.
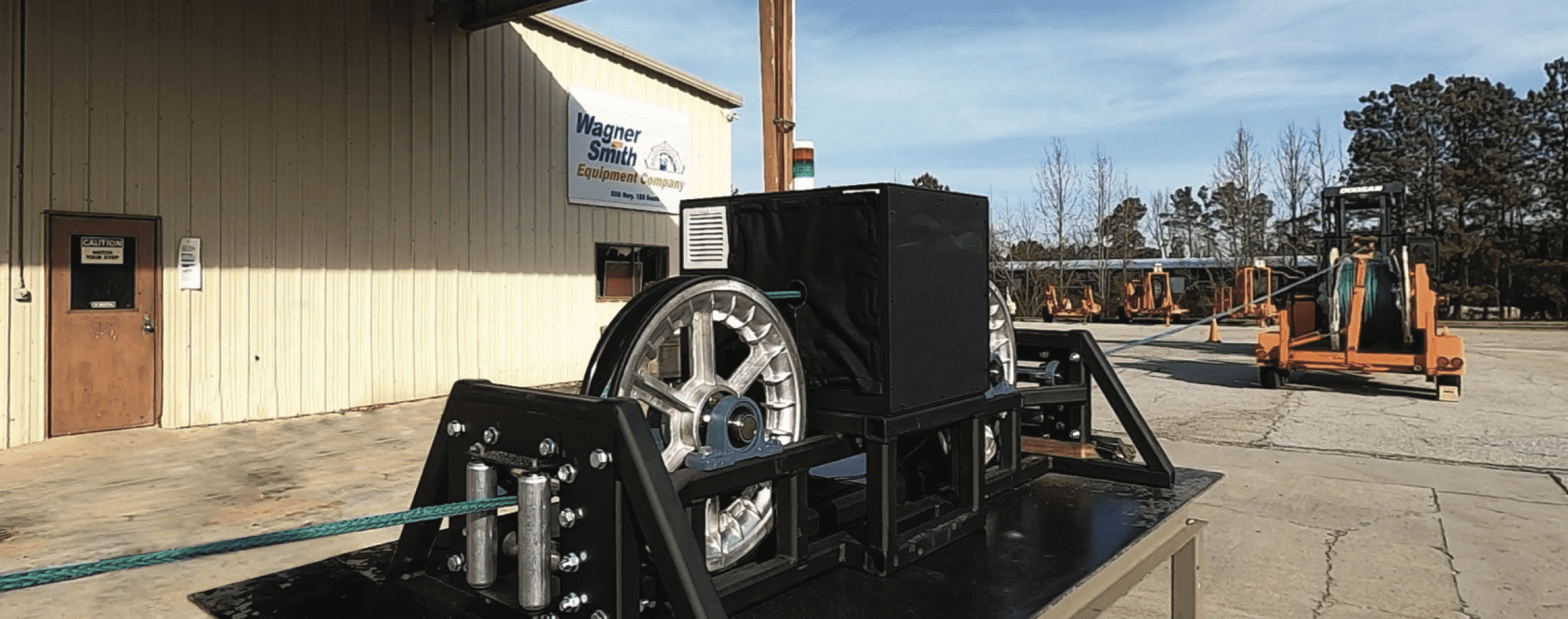
About Wagner - Smith
Established in 1917, Wagner-Smith Equipment has been synonymous with line-stringing equipment for as long as the industry has existed. As a trailblazer for generations, the company has excelled in designing, producing, renting, and servicing overhead and underground line-stringing equipment.
Want to deep in a little more?
Want to deep in a little more?
Download the full case study and see how we can help in your next project.
Download the full case study and see how we can help in your next project.
Download the full case study and see how we can help in your next project.